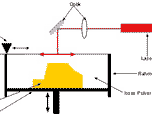
|
Bei diesem Verfahren werden Pulverschichten stufenweise aufgebaut und dann in weiterer Folge durch Laserstrahlen gebunden.
Das Basismaterial ist ein Pulver (Metall, Kunststoff oder Sand), dessen Partikel durchschnittlich 50 μm groß sind. Das Pulver wird schichtweise aufgetragen. Nachdem eine neue Schicht aufgetragen wurde, wird ein Querschnitt des CAD-Modells mittels eines CO2-Lasers auf diese Schicht übertragen. Der Laser schmilzt das Pulver sodass es aushärtet. Durch diese Bestrahlung steigt die Temperatur des Pulvers über den Glaspunkt und benachbarte Partikel fließen zusammen. Diesen Prozess nennt man Sinterung.
Die Temperatur während des Sinterprozesses bleibt konstant knapp unter der Schmelzgrenze des verwendeten Materials. Somit müssen durch die Temperatur des Lasers die Stellen, die verfestigt werden sollen, nur leicht erwärmt werden um das Material zum Schmelzen zu bringen und so zu verfestigen.
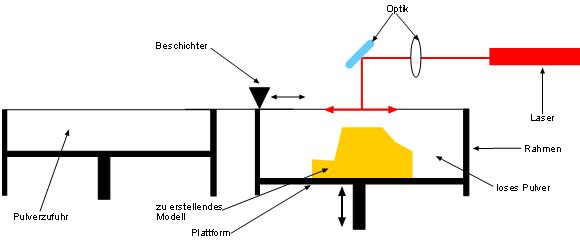
Abb.: Der Beschichter überträgt eine neue Schicht aus der Pulverzufuhr auf das zu erstellende Modell. Ein Scanner überträgt die Laserstrahlen auf die Schicht, diese härtet aus und das Modell wird um eine Schicht abgesenkt. Dann wird eine neue Pulverschicht aus der Pulverzufuhr aufgetragen.
Klassisches SLS: Pulverkörner werden nur teilweise geschmolzen (Flüssigkeitsphasensinterprozess)
DMLS (= Direct Metal Laser Sintering): Bei dieser Methode verwendet man SLM (Selektives Laser Melting), wobei hier das gesamte Pulver geschmolzen wird. Hierfür wird meist ein cw-Laser verwendet.
Lasermikrosintern: Dieses Verfahren wird für die Herstellung von Mikrostrukturen eingesetzt. Hier wird ein Nd:YAG-Laser verwendet, der kurze Pulse verwendet. Mit Hilfe dieses Verfahrens kann Nanopulver zu Modellen verarbeitet werden, deren Auflösung genauer als 30 μm ist. Die Sinterung findet in diesem Fall in einer Vakuumkammer statt.
DMLS (= Direct Metal Laser Sintering): Bei dieser Methode verwendet man SLM (Selektives Laser Melting), wobei hier das gesamte Pulver geschmolzen wird. Hierfür wird meist ein cw-Laser verwendet.
Lasermikrosintern: Dieses Verfahren wird für die Herstellung von Mikrostrukturen eingesetzt. Hier wird ein Nd:YAG-Laser verwendet, der kurze Pulse verwendet. Mit Hilfe dieses Verfahrens kann Nanopulver zu Modellen verarbeitet werden, deren Auflösung genauer als 30 μm ist. Die Sinterung findet in diesem Fall in einer Vakuumkammer statt.
- Durchlaufzeit: je nach Modellgröße unterschiedlich, aber mindestens 4 Tage Arbeitszeit
- Präzision: +/- 0,25 % (mindestens +/- 2 mm)
- Dicke der Wände: 1mm, lebende Gelenke können bis 0,3 mm klein sein
- Bauteilgröße: Die Größe des Behälters, in dem das Modell aufgebaut wird beträgt 700 mm x 380 mm x 580 mm. Wird das Modell in Unterteile geteilt, können auch größere Modelle erzeugt werden.
- Oberflächenstruktur: Modelle, die durch SLS erzeugt werden, haben typischerweise eine körnige Oberfläche. Es besteht jedoch die Möglichkeit, diese Oberfläche zu verfeinern, z.B. mit Sandstrahlen (das Modell wird mit Sand abgeblasen), Einfärben (Imprägnieren), Anmalen oder Überziehen.
- Schichtdicke: 0,1 mm – 0,2 mm
- Vorteil gegenüber SLA: Das Modell ist schneller fertig.
- Industriedesign: Hier wird SLS für Designstudien bzw. als Anschauungsmuster für Designer verwendet. Die Vorteile hierbei sind die detailgetreue Darstellung, die Schnelligkeit und die günstigen Herstellungskosten.
- Entwicklung: Man kann die Funktion von Teilen schon sehr bald preisgünstig testen (Funktionstests). Die durch SLS entstandenen Teile werden auch im Musterbau verwendet.
- Formenbau: Die entstandenen Modelle werden als Anschauungsmuster verwendet, Zusammenhänge selbst können geprüft werden und inwieweit sich diese auf das fertige Werkzeug auswirken.
- Vorverkauf: Hier werden die Modelle oft als Fotomodelle verwendet, sodass die Werbebroschüren bereits schon vor der Fertigstellung des endgültigen Produkts hergestellt werden können. Hierfür wird die Oberfläche des SLS-Modells entsprechend nachbearbeitet.
- Kleinserien: Teilweise findet SLS auch Einsatz in der Fertigung von Serienteilen. Jedoch rentiert sich dies nur, wenn die Teile entsprechend klein sind. Der Vorteil hierfür liegt darin, dass die Teile innerhalb weniger Arbeitstage verfügbar sind.